Wave Energy
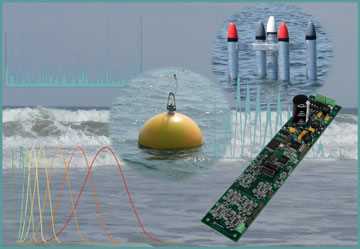
Wave Energy Conversion Systems Designed for Sensor Buoys
Electro Standards Laboratories' (ESL) R&D Engineering Services Group is designing Ocean Wave Energy Harvesting Systems for Sensor Buoys.
The targeted applications for this technology include:
- Recharging stations for UUV (Unmanned Underwater Vehicles)
- Replacement for solar power
- Augmentation of solar power
- Elimination of batteries
- Sonar listening stations
- Weather monitoring buoys
- Wave monitoring buoys
- Tsunami warning stations
- Port monitoring buoys
Wave Energy Technology Goals
- Automatic wave energy harvesting
- Works with drifting or moored operation
- Low acoustic noise
- Stealthy operation (acoustic and visual)
- Wide band response to wave period
- Elimination of batteries
- Enhanced functionality, higher performance and continuous operation
Funding Sources for Wave Energy Research
- Office of Naval Research
- Space and Naval Warfare Systems Command
- Rhode Island Collaborative Research Grant from the Rhode Island
- Science and Technology Council (STAC)
Electro Standards' Team Approach
Scientists at ESL and in the Ocean Engineering Department at the University of Rhode Island (URI) have combined expertise in marine hydrodynamics, electrical generators, advanced controls and dynamics. This team has worked collaboratively to improve the design and performance of wave energy harvesting devices.
Small Spar Buoy
This project was to devise a means of energy harvesting for a small diameter buoy free floating on the ocean surface. The buoy would contain an antenna on the upper portion and electronics for remote communications and sensing. The design would ensure that the buoy produce enough energy so that more than 4 milliwatts of power would be available at an instance. The required battery storage capacity would be at least 60 joules. Energy storage could include the use of a rechargeable battery. The ESL-URI team greatly extended both design concepts and theoretical analyses typically proposed for such systems and performed detailed numerical modeling that featured a wave-to-wire model of the power generation system in ocean sea states. For more details review a report entitled Ocean Wave Energy Harvesting Buoy for Sensors by Steven P. Bastien and Raymond B Sepe, Jr. of Electro Standards Laboratories and Annette R. Grilli, Stephan T. Grilli and Malcolm L. Spaulding of the University of Rhode Island.
Direct Drive System
The Direct Drive System developed by ESL and URI employs small electric generators that are directly driven via a surface buoy's wave-induced heave motion. This system provides power from the differential motion between the buoy float and a submerged resistant plate. This configuration provides reliable operation without the need for additional gearing and has the ability to harness electrical power in the 1 to 10 Watt range in small sea states (WMO Sea State 1: Calm). The buoy response in the Direct Drive System is designed to match a wide range of expected ocean wave spectra based on the deployment location. Direct Drive of the system with wave motion results in broad band response with high efficiency. Other benefits of this system include low acoustic noise and stealthy operation.
Resonant Drive System
The Resonant Drive System developed by ELectro Standards Laboratories and the University of Rhode Island employs small electric generators that are resonantly driven via a surface buoy's wave-induced heave motion. This system amplifies the generator's armature motion at the peak period of the sea state (WMO Sea State 1: Calm). The buoy response in the Resonant Drive System is designed to match the expected ocean wave spectrum based on the deployment location. The benefits of the resonant system inlcude enhanced functionality, higher performance and continuous operation. The buoy is completely sealed with no external moving parts.
Scale Model Testing
Scale model testing of the Direct Drive System and Resonant Drive Systems has been performed in the URI Department of Ocean Engineering wave tank as well as at the mouth of Rhode Island's Narragansett Bay. ESL's model simulations have shown good agreement with the scale model tests. This small buoy sensor system generates and accumulates energy that can be used to indefinitely power remote buoys equipped with sensor arrays as well as electronics for processing and communications. This power source can be used to minimize the size of batteries or to eliminate the need for batteries if supercapacitors are used. The buoy system design is customized and scalable (1-250 W) and can be suited to moored or drifting applications.
There are three parts to Ocean Wave Energy Harvesting Systems:
- Harnessing the energy
- Converting the energy
- Storing the energy
Electro Standards Laboratories is utilizing the ULTIMO, Lithium Ion Capacitor (LIC) from JSR Micro for energy storage
- High cycle life, up to 1 million cycles
- Very low self discharge
- High energy density, 14Wh/kg or 25Wh/L
- High power density, 5kW/kg or 8kW/L
- Light weight and low volume
- High energy content (2200F cell)
- ~1 amp-hr
- ~3 watt-hrs
- ~10.5kJ
- High efficiency at low currents, up to 98%
- High current capability, up to 480 amps or 200 amp continuous
- No Thermal runway
- Low Lithium content
- Environmentally safe
- Wide temperature performance
- (-20°C to 70°C)
- Quick charge times
- Space efficient laminate form factor
- Safe and reliable
- Power providing asymmetric design
Furthering the Science
Targeted applications for this technology include:
- Recharging stations for Unmanned Underwater Vehicles
- Replacement or augmentation for solar power
- Elimination of batteries
- Sonar listening stations
- Weather monitoring buoys
- Wave monitoring buoys
- Tsunami warning stations
- Port monitoring buoys
White Papers & Information:
Click on the following link to download white paper.
Wave Energy Conversion Systems Designed for Sensor Buoys
For More Information:
Dr. Raymond Sepe Jr., is the program's lead scientist. For more information on Ocean Wave Energy Opportunities with Electro Standards Laboratories, call 401.943.1164, or email eslab@electrostandards.com